بازرسی و کنترل کیفیت رنگ و سندبلاست
فلزات بطور خالص در حالت ناپایدار قرار دارند ، میل طبیعی این عناصر در تبدیل شد ن به اکسیدها و پایدار شدنشان ، معضل بزرگ امروزه در سراسر دنیاست . چه بسا هزینه های هنگفتی صرف مطالعات و تحقیقات در این زمینه گردیده و می گردد و چه بسا حوادث ناگواری بدلیل خوردگی و اکسید شدن فلزات اتفاق افتاده است .
آماده سازی سطح برای رنگ آمیزی
تمیز کردن سطح از زنگ زدگی و آلودگیهای دیگر نظیر گریس ، روغن و گرد و خاک قبل از رنگ آمیزی بسیار مهم است . اگر از بهترین رنگ استفاده شود و به بهترین روش اجرا شود ولی آماده سازی سطح خوب نباشد رنگ در مدت کوتاهی از بین می رود .
انواع روشهای آماده سازی
(HAND CLEANING) ۱ – تمیز کردن با دست
(WATER BLAST CLEANING) ۲ – آماده سازی سطح به روش پاشیدن آب با فشار
(SAND BLAST) ۳ – آماده سازی سطح به روش پاشیدن ماسه با هوای فشرده
(SHOT BLAST) ۴ – آماده سازی سطح به روش شات بلاست
آماده سازی سطح به روش پاشیدن ماسه با هوای فشره ( SAND BLAST )
سندبلاست به دو دلیل مهم صورت میگیرد :
الف – از بین بردن کلیه آلودگیهای سطح
ب – زبر کردن سطح برای بهبود چسبند گی پرایمر هر قدر اندازه ماسه ها استانداردتر و فشارهوا بالای ٧ بار باشد سطح سندبلاست شده زبرتر و چسبندگی ایده آل تر خواهد بود . در این روش دستگاه تولید هوای فشرده (کمپرسور) هوا را با شیلنگ به دیگ سندبلاست میرساند . از دیگ سندبلاست ماسه به صورت کنترل شده در مسیر هوای فشرده قرار م ی گیرد و از نازل خروجی با فشار خارج م یشود . چنانچه نازل خروجی را به طرف سطح فلزی گرفته شود باعث تمیز شدن و زبر شدن سطح می شود . قبل از شروع سندبلاست سطح فلز باید بازرسی شده و آلودگ یهای روغنی با تینر تمیز شود.
مواردی که در سندبلاست باید مد نظر قرار گیرند :
الف : هوای فشرده باید کاملا خشک و عاری از روغن باشد.
ب : اندازه ماسه ها باید بین 0.3 الی 3 میلیمتر باشد.
ج : سطح سندبلاست شده باید با هوای فشرده خوب تمیز و عاری از گرد و خاک شود.
د : حداقل زبری سطح سندبلاست شده باید ٢۵ میکرون باشد که باید بوسیله دستگاه زبری سنج اندازه گیری شود.
رنگ آمیزی
پوشش (رنگ) : اصولا رنگ به مخلوطی گفته می شود که بتواند انتظارات ما را در مورد تزئین و حفاظت سطح برآورده کند . عمومًا پوشش عالی از اختلاط موادی بنام رزین (RESIN) رنگدانه (PIGMENT) حلال (SOLVENT) و مواد افزودنی (ADDITIVES) بدست می آید.پایه اصلی رنگ را رزین تشکیل می دهد . رزین وظایف عمده ای را بعهده دارد . ایجاد فیلم نفوذ ناپذیر روی سطح مورد نظر از مهمترین وظایف رزین است ، از وظایف دیگر رزین چسبندگی به سطح است . سطح فلز هر چه تمیز تر باشد چسبندگی به طریق شیمیایی و قطبی افزایش می یابد و هر چه سطح فولاد زبرتر باشد چسبندگی رزین به طریق مکانیکی افزایش پیدا می کند .
تأثیر شرایط جوی در کیفیت اجرای رنگ
۱ – چنانچه در هوای طوفانی رنگ اجرا شود موارد ذیل اتفاق میافتد.
الف – سطوح رنگ که هنوز خشک نشده به گرد و خاک آلوده میشود.
ب – گرد و خاک روی سطوحی که در حال رنگ آمیزی است نشس ته و باعث عدم چسبندگی لایه رنگ می شود.
ج – گرد و خاک در ظرف رنگ وارد شده و سبب گرفتگی نازل رنگپاش م یگردد.
٢- رنگ آمیزی در هوای بارانی روی لایه قبلی چسبندگی نداشته و از سطح جدا میشود.
روشهای رنگ آمیزی
١- رنگ آمیزی با قلم مو
٢- رنگ آمیزی با غلطک دستی
٣- رنگ آمیزی به روش غوطه وری
۴ – رنگ آمیزی با دستگاه رنگپاش (پیستوله)
۵- رنگ آمیزی به روش پاششی بدون هوا ( AIR LESS )
روش حمل و نقل قطعات رنگ شده
١- مدت زمان خشک شدن فیلم رنگ را سازنده تعیین م یکند.
٢- برای جابجایی ، بارگیری و تخل یه قطعات رنگ شده باید از سیم بکسلهای بافته شده غیر آلی استفاده شود .
٣- قطعات رنگ شده را در هر شرایطی باید روی قطعات چوبی گذاشته شود.
بازرسی
بازرسی و کنترل کیفیت رنگ
١- کلیه بازرسیها باید توسط بازرس طبق شرایط زیر باشد :
الف – بازرس باید ملزومات قبل از سندبلاست از قبیل سنگ زنی جوشها و لب ه های تیز برداشتن آلودگیهای گریس و غیره از سطح را کنترل نماید .
ب – خصوصیات و کیفیت آماد ه سازی سطح را تشخیص و با ابزار آلات مخصوص ، آماده سازی سطح ورنگ آمیزی را کنترل نماید .
ج – تکنیکهای اجرای رنگ و خصوصیات انواع رنگ ها را کنترل نماید
٢- اگر کیفیت آماده سازی سطح مطلوب باشد . دمای سطح بالاتر از ۶٠ درجه سانتیگراد نبوده شرایط جوی مساعد باشد . بازرس دستور مخلوط کردن رنگ را م یدهد.
٣- تاریخ مصرف رنگ را کنترل نماید .
۴ – حلبهای رنگ پس از باز شدن باید بازرسی شوند تا از کیفیت مناسب آنها اطمینان حاصل شود.
انواع روشهای تست چسبندگی رنگ
ما در این قسمت درمورد روش اجرایی و معیار پذیرش تست های متداول چسبندگی رنگ در صنعت کشور یعنی ایکس کات (X-CUT) و کراس کات (CROSS-CUT) را طبق ASTM D 3359 به صورت ساده و کاربردی صحبت می کنیم.
به طور کلی سه روش اصلی برای تعیین میزان چسبندگی رنگ وجود دارد که عبارتند از :
روش تست (X-Cut):
برای انجام تست چسبندگی (کراس کات) باید سطحی انتخاب شود که عاری ازخط و خش باشد.
ازتمیز وخشک بودن سطح اطمینان حاصل کنید . دمای بالا ورطوبت زیاد برچسبندگی فیلم تاثیر می گذارد. دو برش بطول تقریبی 1.5 اینچ (40میلیمتر) برسطح مورد نظرایجاد نمایید بطوریکه از وسط یکدیگر بگذرند بطوری که زاویه بین آنها 30 تا 45 درجه باشد.
بریدگی و شکاف ایجاد شده را به لحاظ رویت انعکاس نور از سطح فلز مورد بازرسی قرار دهید تا مطمئن شوید که فیلم پوشش رنگ کاملا نفوذ کرده است. باید دقت کنید که اگر سطح فلز رویت نشد، برش X جدیدی دیگری در محل دیگری ایجاد نمایید.
توجه: عمل برش باید در یک مرحله صورت گیرد و عمیق تر نمودن شکاف قبلی صحیح نیست.
دو دور کامل از چسب نواری را جدا کنید و یک تکه 3 اینچی (75 میلیمتر) را از آن ببرید.
وسط چسب را در نقطه برخورد برشها قرار دهید و سپس با انگشت آنرا روی برش بچسبانید و آنرا کامل بر سطح بچسبانید.
بعداز 90±30 ثانیه از اعمال چسب، نوار را به سرعت از روی سطح بکنید. اینکارباید بدون تکان اضافه دست انجام شود و همچنین نوار بر روی خودش هنگام کندن زاویه 180 درجه داشته باشد.
حالا محل برش X را از لحاظ جدایش از سطح فلز با استفاده از مقیاس های که در زیر آمده مورد برسی قرار دهید:
۵A : بدون هیچ گونه جدایش
۴A : مقدار کمی کنده شدن یا جدایش در امتداد بریدگی ها و یا در محل برخوردشان
۳A: جدایش ناصاف و بریده بریده در امتداد بریدگی ها تا ۱.۶ میلیمتر در طرف دیگر
۲A : جدایش ناصاف و بریده بریده در امتداد بیشتر بریدگی ها تا ۳.۲ میلیمتر در طرف دیگر
۱A : جدایش در اکثر نواحی برش X در زیرنوار
۰A : جدایش دورتر از ناحیه X
برای اطمینان از چسبندگی سایر نقاط، به تعداد کافی در محل های دیگر از سطح، تست را تکرار کنید.
روش : Pull Off
در این روش ابتدا یک صفحه نازک به اسم Dolly ، با چسب به سطح رنگ مورد آزمایش محکم می جسبانیم.
سپس دستگاه تست چسبندگی به روش Pull Off Testing را به این صفحه گیر میدهیم و با چرخاندن اهرم به صفحه نیروی رو به بالا وارد میکنیم .
نیرو را آنقدر اضافه میکنیم که صفحه به هماره لایه رنگ زیرین آن از سطح پایه جدا شود. در این زمان میزان نیروی وارد به صفحه در آخرین لحظه معیار محاسبات ما خواهد بود.
تست کراس کات (CROSS-CUT) :
به کمک ابزار برش کراس کات، دو شبکه برش متقاطع به طول تقریبی ۲۰ میلی متر بر روی فیلم رنگ ایجاد کنید. برش باید به گونه ای باشد که در همان مرتبه اول، فیلم رنگ را برش داده و به سطح فلز رسیده باشد. بدون ابزار برش کراس کات هم می توان با استفاده از یک تیغ تیز، این برش ها را انجام داد. در این صورت برای رنگ های تا ضخامت ۵۰ میکرون، ۱۱ برش با فاصله یک میلی متر از هم و برای رنگ های از ضخامت ۵۰ تا ۱۲۵ میکرون، ۶ برش با فاصله ۲ میلی متر از هم به صورت متقاطع ایجاد می کنیم.
به کمک یک برس نرم، روی بریدگی های شبکه ای را تمیز می کنیم.
دو دور کامل از چسب نواری را جدا کرده و یک تکه ۷۵ میلیمتری از آن را ببرید.
وسط چسب را در محل تقاطع برش ها قرار داده و دو طرف آن را به سمت زاویه کوچکتر تقاطع بچسبانید. سپس با پاک کن روی آن مالش دهید تا کاملاً به سطح بچسبد.
پس از گذشت ۳۰±۹۰ ثانیه، چسب را به سرعت و بدون تکان اضافه دست از روی سطح بکنید.
محل برش را از لحاظ جدایش رنگ از سطح فلز با استفاده از طبقه بندی شکل زیر برای مقدار جدایش در تست کراس کات مورد بازرسی قرار دهید. معیار پذیرش تست چسبندگی در اسپک پروژه مشخص می شود. در بیشتر پروژه ها معیار پذیرش سطح ۴B و ۵B تعیین می شود.
بازرسی و کنترل کیفیت رنگ و سندبلاست
فلزات بطور خالص در حالت ناپایدار قرار دارند ، میل طبیعی این عناصر در تبدیل شد ن به اکسیدها و پایدار شدنشان ، معضل بزرگ امروزه در سراسر دنیاست . چه بسا هزینه های هنگفتی صرف مطالعات و تحقیقات در این زمینه گردیده و می گردد و چه بسا حوادث ناگواری بدلیل خوردگی و اکسید شدن فلزات اتفاق افتاده است .
آماده سازی سطح برای رنگ آمیزی
تمیز کردن سطح از زنگ زدگی و آلودگیهای دیگر نظیر گریس ، روغن و گرد و خاک قبل از رنگ آمیزی بسیار مهم است . اگر از بهترین رنگ استفاده شود و به بهترین روش اجرا شود ولی آماده سازی سطح خوب نباشد رنگ در مدت کوتاهی از بین می رود .
انواع روشهای آماده سازی
(HAND CLEANING) 1- تمیز کردن با دست
(WATER BLAST CLEANING) 2- آماده سازی سطح به روش پاشیدن آب با فشار
(SAND BLAST) 3- آماده سازی سطح به روش پاشیدن ماسه با هوای فشرده
(SHOT BLAST) 4- آماده سازی سطح به روش شات بلاست
آماده سازی سطح به روش پاشیدن ماسه با هوای فشره ( ( SAND BLAST
سندبلاست به دو دلیل مهم صورت میگیرد :
الف – از بین بردن کلیه آلودگیهای سطح
ب – زبر کردن سطح برای بهبود چسبند گی پرایمر هر قدر اندازه ماسه ها استانداردتر و فشارهوا بالای ٧ بار باشد سطح سندبلاست شده زبرتر و چسبندگی ایده آل تر خواهد بود . در این روش دستگاه تولید هوای فشرده (کمپرسور) هوا را با شیلنگ به دیگ سندبلاست میرساند . از دیگ سندبلاست ماسه به صورت کنترل شده در مسیر هوای فشرده قرار م ی گیرد و از نازل خروجی با فشار خارج م یشود . چنانچه نازل خروجی را به طرف سطح فلزی گرفته شود باعث تمیز شدن و زبر شدن سطح می شود . قبل از شروع سندبلاست سطح فلز باید بازرسی شده و آلودگ یهای روغنی با تینر تمیز شود.
مواردی که در سندبلاست باید مد نظر قرار گیرند :
الف : هوای فشرده باید کاملا خشک و عاری از روغن باشد.
ب : اندازه ماسه ها باید بین 0.3 الی 3 میلیمتر باشد.
ج : سطح سندبلاست شده باید با هوای فشرده خوب تمیز و عاری از گرد و خاک شود.
د : حداقل زبری سطح سندبلاست شده باید ٢۵ میکرون باشد که باید بوسیله دستگاه زبری سنج اندازه گیری شود.
رنگ آمیزی
پوشش (رنگ) : اصولا رنگ به مخلوطی گفته می شود که بتواند انتظارات ما را در مورد تزئین و حفاظت سطح برآورده کند . عمومًا پوشش عالی از اختلاط موادی بنام رزین (RESIN) رنگدانه (PIGMENT) حلال (SOLVENT) و مواد افزودنی (ADDITIVES) بدست می آید.پایه اصلی رنگ را رزین تشکیل می دهد . رزین وظایف عمده ای را بعهده دارد . ایجاد فیلم نفوذ ناپذیر روی سطح مورد نظر از مهمترین وظایف رزین است ، از وظایف دیگر رزین چسبندگی به سطح است . سطح فلز هر چه تمیز تر باشد چسبندگی به طریق شیمیایی و قطبی افزایش می یابد و هر چه سطح فولاد زبرتر باشد چسبندگی رزین به طریق مکانیکی افزایش پیدا می کند .
تأثیر شرایط جوی در کیفیت اجرای رنگ
1- چنانچه در هوای طوفانی رنگ اجرا شود موارد ذیل اتفاق میافتد.
الف – سطوح رنگ که هنوز خشک نشده به گرد و خاک آلوده میشود.
ب – گرد و خاک روی سطوحی که در حال رنگ آمیزی است نشس ته و باعث عدم چسبندگی لایه رنگ می شود.
ج – گرد و خاک در ظرف رنگ وارد شده و سبب گرفتگی نازل رنگپاش م یگردد.
٢- رنگ آمیزی در هوای بارانی روی لایه قبلی چسبندگی نداشته و از سطح جدا میشود.
روشهای رنگ آمیزی
١- رنگ آمیزی با قلم مو
٢- رنگ آمیزی با غلطک دستی
٣- رنگ آمیزی به روش غوطه وری
۴- رنگ آمیزی با دستگاه رنگپاش (پیستوله)
۵- رنگ آمیزی به روش پاششی بدون هوا ( AIR LESS )
روش حمل و نقل قطعات رنگ شده
١- مدت زمان خشک شدن فیلم رنگ را سازنده تعیین م یکند.
٢- برای جابجایی ، بارگیری و تخل یه قطعات رنگ شده باید از سیم بکسلهای بافته شده غیر آلی استفاده شود .
٣- قطعات رنگ شده را در هر شرایطی باید روی قطعات چوبی گذاشته شود.
بازرسی
بازرسی و کنترل کیفیت رنگ
١- کلیه بازرسیها باید توسط بازرس طبق شرایط زیر باشد :
الف – بازرس باید ملزومات قبل از سندبلاست از قبیل سنگ زنی جوشها و لب ه های تیز برداشتن آلودگیهای گریس و غیره از سطح را کنترل نماید .
ب – خصوصیات و کیفیت آماد ه سازی سطح را تشخیص و با ابزار آلات مخصوص ، آماده سازی سطح ورنگ آمیزی را کنترل نماید .
ج – تکنیکهای اجرای رنگ و خصوصیات انواع رنگ ها را کنترل نماید
٢- اگر کیفیت آماده سازی سطح مطلوب باشد . دمای سطح بالاتر از ۶٠ درجه سانتیگراد نبوده شرایط جوی مساعد باشد . بازرس دستور مخلوط کردن رنگ را م یدهد.
٣- تاریخ مصرف رنگ را کنترل نماید .
۴- حلبهای رنگ پس از باز شدن باید بازرسی شوند تا از کیفیت مناسب آنها اطمینان حاصل شود.
انواع روشهای تست چسبندگی رنگ
ما در این قسمت درمورد روش اجرایی و معیار پذیرش تست های متداول چسبندگی رنگ در صنعت کشور یعنی ایکس کات (X-CUT) و کراس کات (CROSS-CUT) را طبق ASTM D 3359 به صورت ساده و کاربردی صحبت می کنیم.
به طور کلی سه روش اصلی برای تعیین میزان چسبندگی رنگ وجود دارد که عبارتند از :
روش تست (X-Cut):
برای انجام تست چسبندگی (کراس کات) باید سطحی انتخاب شود که عاری ازخط و خش باشد.
ازتمیز وخشک بودن سطح اطمینان حاصل کنید . دمای بالا ورطوبت زیاد برچسبندگی فیلم تاثیر می گذارد. دو برش بطول تقریبی 1.5 اینچ (40میلیمتر) برسطح مورد نظرایجاد نمایید بطوریکه از وسط یکدیگر بگذرند بطوری که زاویه بین آنها 30 تا 45 درجه باشد.
بریدگی و شکاف ایجاد شده را به لحاظ رویت انعکاس نور از سطح فلز مورد بازرسی قرار دهید تا مطمئن شوید که فیلم پوشش رنگ کاملا نفوذ کرده است. باید دقت کنید که اگر سطح فلز رویت نشد، برش X جدیدی دیگری در محل دیگری ایجاد نمایید.
توجه: عمل برش باید در یک مرحله صورت گیرد و عمیق تر نمودن شکاف قبلی صحیح نیست.
دو دور کامل از چسب نواری را جدا کنید و یک تکه 3 اینچی (75 میلیمتر) را از آن ببرید.
وسط چسب را در نقطه برخورد برشها قرار دهید و سپس با انگشت آنرا روی برش بچسبانید و آنرا کامل بر سطح بچسبانید.
بعداز 90±30 ثانیه از اعمال چسب، نوار را به سرعت از روی سطح بکنید. اینکارباید بدون تکان اضافه دست انجام شود و همچنین نوار بر روی خودش هنگام کندن زاویه 180 درجه داشته باشد.
حالا محل برش X را از لحاظ جدایش از سطح فلز با استفاده از مقیاس های که در زیر آمده مورد برسی قرار دهید:
5A : بدون هیچ گونه جدایش
4A : مقدار کمی کنده شدن یا جدایش در امتداد بریدگی ها و یا در محل برخوردشان
3A: جدایش ناصاف و بریده بریده در امتداد بریدگی ها تا 1.6 میلیمتر در طرف دیگر
2A : جدایش ناصاف و بریده بریده در امتداد بیشتر بریدگی ها تا 3.2 میلیمتر در طرف دیگر
1A : جدایش در اکثر نواحی برش X در زیرنوار
0A : جدایش دورتر از ناحیه X
برای اطمینان از چسبندگی سایر نقاط، به تعداد کافی در محل های دیگر از سطح، تست را تکرار کنید.
روش : Pull Off
در این روش ابتدا یک صفحه نازک به اسم Dolly ، با چسب به سطح رنگ مورد آزمایش محکم می جسبانیم.
سپس دستگاه تست چسبندگی به روش Pull Off Testing را به این صفحه گیر میدهیم و با چرخاندن اهرم به صفحه نیروی رو به بالا وارد میکنیم .
نیرو را آنقدر اضافه میکنیم که صفحه به هماره لایه رنگ زیرین آن از سطح پایه جدا شود. در این زمان میزان نیروی وارد به صفحه در آخرین لحظه معیار محاسبات ما خواهد بود.
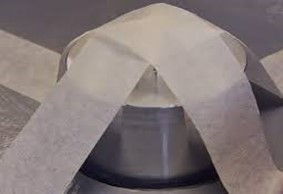
تست کراس کات (CROSS-CUT) :
به کمک ابزار برش کراس کات، دو شبکه برش متقاطع به طول تقریبی ۲۰ میلی متر بر روی فیلم رنگ ایجاد کنید. برش باید به گونه ای باشد که در همان مرتبه اول، فیلم رنگ را برش داده و به سطح فلز رسیده باشد. بدون ابزار برش کراس کات هم می توان با استفاده از یک تیغ تیز، این برش ها را انجام داد. در این صورت برای رنگ های تا ضخامت ۵۰ میکرون، ۱۱ برش با فاصله یک میلی متر از هم و برای رنگ های از ضخامت ۵۰ تا ۱۲۵ میکرون، ۶ برش با فاصله ۲ میلی متر از هم به صورت متقاطع ایجاد می کنیم.
به کمک یک برس نرم، روی بریدگی های شبکه ای را تمیز می کنیم.
دو دور کامل از چسب نواری را جدا کرده و یک تکه ۷۵ میلیمتری از آن را ببرید.
وسط چسب را در محل تقاطع برش ها قرار داده و دو طرف آن را به سمت زاویه کوچکتر تقاطع بچسبانید. سپس با پاک کن روی آن مالش دهید تا کاملاً به سطح بچسبد.
پس از گذشت ۳۰±۹۰ ثانیه، چسب را به سرعت و بدون تکان اضافه دست از روی سطح بکنید.
محل برش را از لحاظ جدایش رنگ از سطح فلز با استفاده از طبقه بندی شکل زیر برای مقدار جدایش در تست کراس کات مورد بازرسی قرار دهید. معیار پذیرش تست چسبندگی در اسپک پروژه مشخص می شود. در بیشتر پروژه ها معیار پذیرش سطح ۴B و ۵B تعیین می شود.
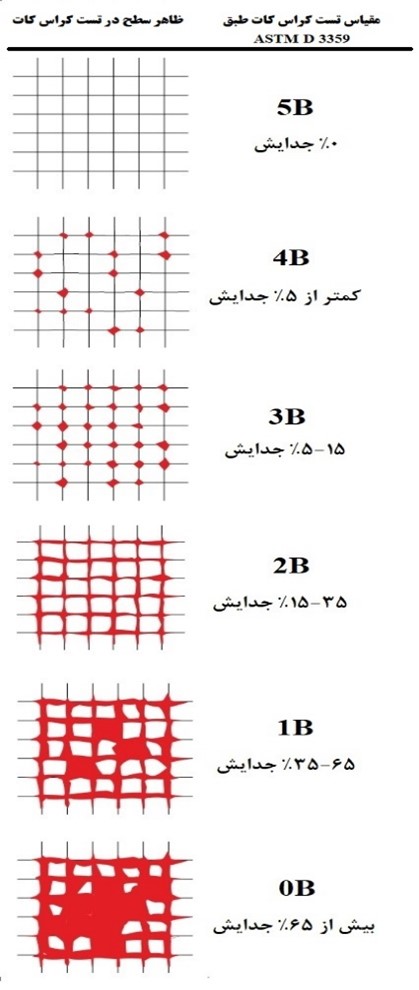